PP Melt-Blown Fabric Production Line

Melt-blown fabric production line which is applied to produce inner filter fabric of mask and protection suit.
This machine consist:
1: polymer feeder
2: molten extruder
3: fiber formation
4: electrostatic electret
5: slitting and winding
Related machine:
1.melt blown fabric recycling machine
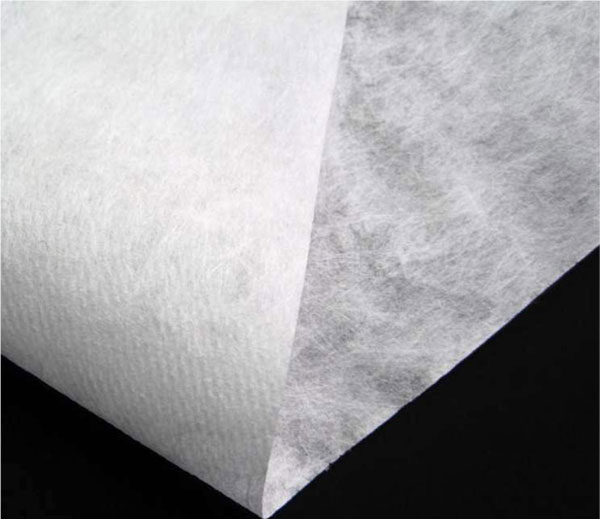
Model | GW600 | GW800 | GW1000 | GW1200 | GW1600 |
Product Width(mm) | 600 | 800 | 1000 | 1200 | 1600 |
Output(kg/24hours) | 400 | 500 | 500 | 750 | 1000 |
Unit Weight(g/m2) | 25-100 | 25-100 | 25-100 | 25-100 | 25-100 |
Filament size(μm) | 2-8 | 2-8 | 2-8 | 2-8 | 2-8 |
BFE Grade | ≥95 | ≥95 | ≥95 | ≥95 | ≥95 |
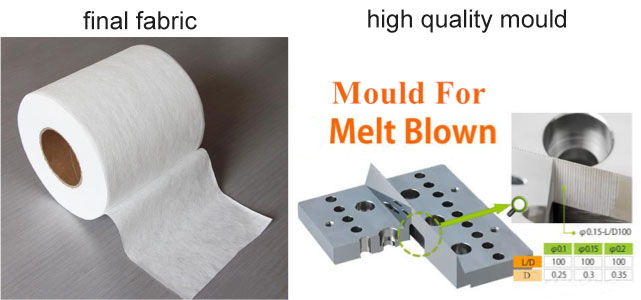
This equipment is equipped with automatic vacuum suction feeding device. Generally, the polymer is made into small spherical and granular slices. When the vacuum device is opened, the raw materials can be fed into the hopper equipped with the extruder.
If the material in the hopper is low, it will fill it up automatically. Otherwise, the material will be broken and the melt spray cloth will become thin or not mesh.
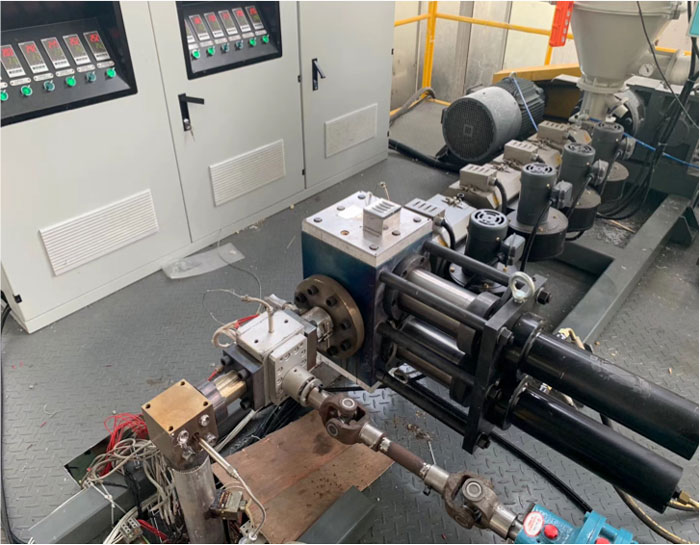
Before the material feed into the extruder, the polymer slice shall be mixed with the necessary raw materials such as additives. After mixing, the polymer slice shall enter the screw extruder and be heated to melt. Pay attention to the heating temperature,User can adjust the temperature and extrusion speed according to the characteristics of the raw materialor accordance with the manufacturer’s recommended parameter Settings, or accordance with the actual production requirements, so that the finished products to meet the user’s requirements.
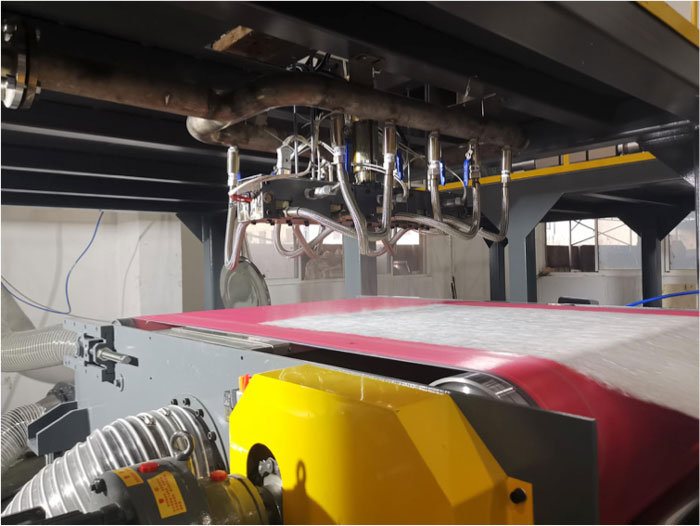
The filtered clean melted pp should pass through the filter screen and then be evenly fed into the spinneret to make the extrusion amount of each spinneret consistenta and stable.
When the alarm rang,user need to stop the machine to check whether there is a fault, check whether the filter screen is blocked, timely troubleshooting problems, so as not to damage the extrusion equipment.When eliminating extruder problems, Check the filter plate of the spinneret,observe whether the holes in the filter plate have impurities that cannot flow normally. The fibers are pulled out from the spinneret by the crosswind, and then cooled.
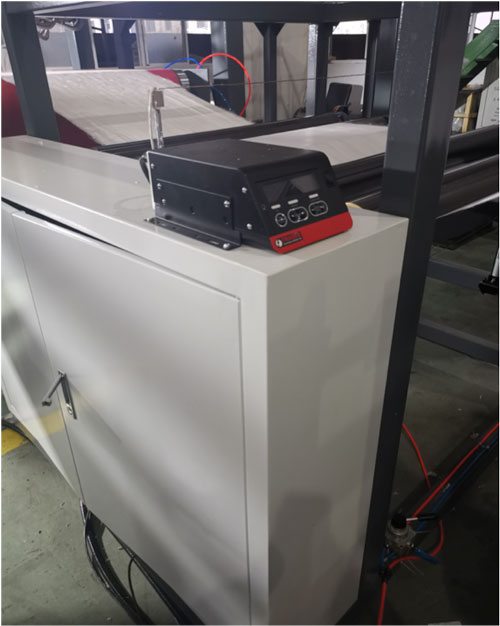
After the net through the electrostatic device, so that the melt – spraying non – woven fabric with static electricity.PM2.5 particles and other isolation mainly through two ways: mechanical blocking and electrostatic adsorption.Among them, mechanical block main
It is to use the small pores of the filter material of mask fiber to block the invasion of bacteria and viruses, but this mechanical blocking effect is very bad for the filtration effect of particles with particle size less than 1 m, so it cannot work
To urification.Therefore, in order to improve the filtration efficiency of the mask, the electrostatic adsorption capacity of the mask can be increased.And increase the capacity of mask electrostatic adsorption, the need to melt spray non – spinning
Cloth filter material for electret treatment.After electret treatment, the surface of the fiber will be charged with a large amount of static electricity
Add breathing resistance.
There is winding equipment at the end of the production line.The fusion-sprayed non-woven fabric is cut and rolled up to the size required for packaging.Winding has tension control device, so that the winding material is always stable,
there is a cutting knife before the winding equipment, which can remove the edge material and cut the size of the fabric to get customized width of the finished product, the distance between the cutting knife can be adjusted according to the production needs.